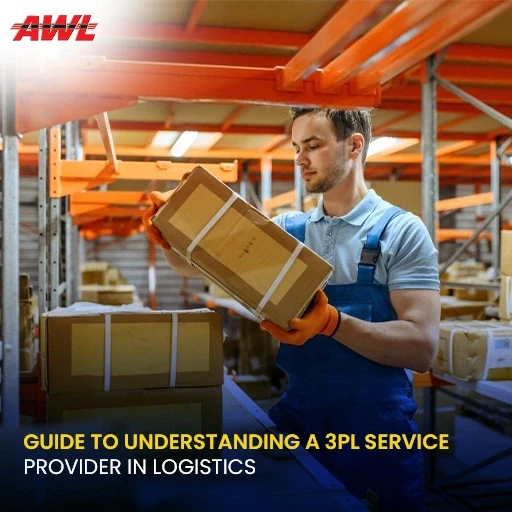
;
25-Sep-2021
Till now, Vaccination is the only action against COVID-19 for saving the assets of our country. Vaccines are one of the most effective preventative technologies in the fight against infectious diseases. No other technology has proven to be as instrumental or cost-effective in saving lives and averting illness from infectious diseases like COVID-19 in the present. Members of AWL INDIA are part of a global community united by a common challenge to save lives. AWL INDIA is consistently transporting life-saving pharma products and vaccines with specially designed superior transport systems and helping in accelerating the rate of vaccination in INDIA.
The vaccine technologies that have driven the public health and economic gains from immunization around the world would not be possible without sustained investment in innovation and the unwavering ambition of dedicated scientists working in universities, research institutions, biotechs, and our own companies.
We are continually exploring new technologies and creating new formulations to transport vaccines and work better to make it easier to reach people regardless of where they live. However, the benefits from these advancements will not be fully realized unless there is also progress in the areas of regulatory convergence and harmonization, facilitated approvals, country-level infrastructure upgrading, sustainable supply chain training, and demand forecasting.
UNICEF is working to buy 1 billion syringes by the end of 2021 for COVID-19 vaccination efforts in countries participating in this cause. Although the vaccines secured by the Facility may vary in their formulation and storage requirements, the syringes will all be of the auto-disable (AD) type, approved by the World Health Organization.
AD syringes are recommended for immunization programs because they are designed to prevent e-use by locking automatically after a single use. They are the best way of ensuring that people receive their shots safely, without a risk of contracting an infection due to contaminated needles. The AD syringes bought for this immense operation are similar to those routinely procured and delivered by UNICEF for the vaccination of children worldwide.
The first level of packaging refers to the vial, ampoule, prefilled syringe, or other containers that are in direct contact with the vaccine. The second level of packaging is what holds the primary container(s) (e.g., cartons containing one or more vials or prefilled syringes of vaccines) and the package insert. The third level of packaging is the outer box or the shipping box containing multiple secondary packaging.
Manufacturers are addressing packaging size concerns while remaining mindful of the diverse needs of frontline healthcare workers for vaccination campaigns. Among other things, manufacturers are converting, when possible, pre-filled syringes, which occupy more volume per dose to single-dose vials, reducing and harmonizing the size of primary, secondary, and tertiary containers, as well as developing multidose vial presentations and combination vaccines. The aim is to make choices available that are easy to transport and administer. This can help reduce wastage rates and increase vaccination coverage, compliance, and safety, making optimal use of existing cold-chain storage in low-resource settings with limited infrastructure.
A controlled-temperature chain is defined as the storage and transport temperatures above the traditional 2-8°C, which may allow product exposure to 40°C for 4 days, before administration, under monitored and controlled conditions, and as appropriate to the stability of the antigen. Vaccines are kept between 2-8°C (36-46°F). This cold chain requires intense logistics in resource-limited settings. This is an important step since the vaccine is not just prone to breakage but also exposed to a higher risk of theft.
This makes it vital to monitor the temperature-controlled vaccine shipment’s status and keep a check on the route/carrier performance. Thus, feeds on live location, temperature, condition, and security are more important than ever to avoid operational disruption. This is where IoT-based sensors help in monitoring live location and condition at a package level.
After this, the vaccines meant to be distributed locally are taken directly to the vaccine centers, and those that have to be moved to another state or country are taken to the airport for loading onto the flight. Then begins an even trickier part of the journey.
Air cargo plays a key role in the distribution of vaccines through well-established temperature-sensitive distribution systems, using cutting-edge technology and procedures.
This capability will prove crucial to the quick and efficient transport of COVID-19 vaccines once available. This will naturally require careful planning by every segment in the entire cargo supply chain to ensure full preparedness when vaccines for COVID-19 are approved and ready for distribution.
To guarantee the quality of the product, vaccines must be handled and transported in line with international regulatory and manufacturers’ requirements, at controlled temperatures, and without delay.
Priorities for developing capacity and resources for vaccine distribution include:
A vaccine’s journey through the supply chain is complex. Because most vaccines are sensitive to heat or light, they must be transported and stored under the correct conditions to maintain their quality and potency. This requires robust and reliable cold chain equipment.
Although cold chain equipment for the purposes of vaccine storage has existed for decades, the equipment standards in countries did not match the pace of vaccine development and availability. Furthermore, older technologies had issues, such as poor temperature control that risked wastage if vaccines were exposed to temperature fluctuations.
However, upgrading thousands of units in health centers across the eligible countries and ensuring that they are properly installed and maintained presented a considerable challenge. It also presented a unique opportunity to move forward with innovations in both equipment and approach.
By investing in new cold chain equipment, countries can ultimately save money over the average 10-year lifespan of the equipment and safeguard vaccines for routine immunization programs through the last mile of their journey.
Read More: Healthcare Logistics